We Make It Possible
E-Commerce Distribution Facility
Hillwood Investment Properties
This state-of-the-art automated robotic sortation (ARS) distribution facility houses specially designed robotics to streamline the sorting and shipping process for a popular e-commerce company.
Overcoming Site Conditions
The facility sits on an 84-acre site on a former golf course. Before starting the structure, our team had to address karst rock conditions. We adapted the common practice of using geopiles to support the weight of the building to using micropiles, which were narrower and more spread out to fill more of the cavernous voids. Our team installed 30 miles of micropiles to support the approximately three million-square-foot distribution facility.
Large-Scale Structure
This build required 3.2 million cubic yards of concrete and 19,000 tons of structural steel. The building required precise measurements for the interior to accommodate its specialized robotic equipment.
Staying on Schedule
Yates Construction used 4D technology as a collaboration and communication tool to visualize the build sequence. Utilizing this technology, we worked with the client and design team to create solutions to challenges and optimize the construction schedule.
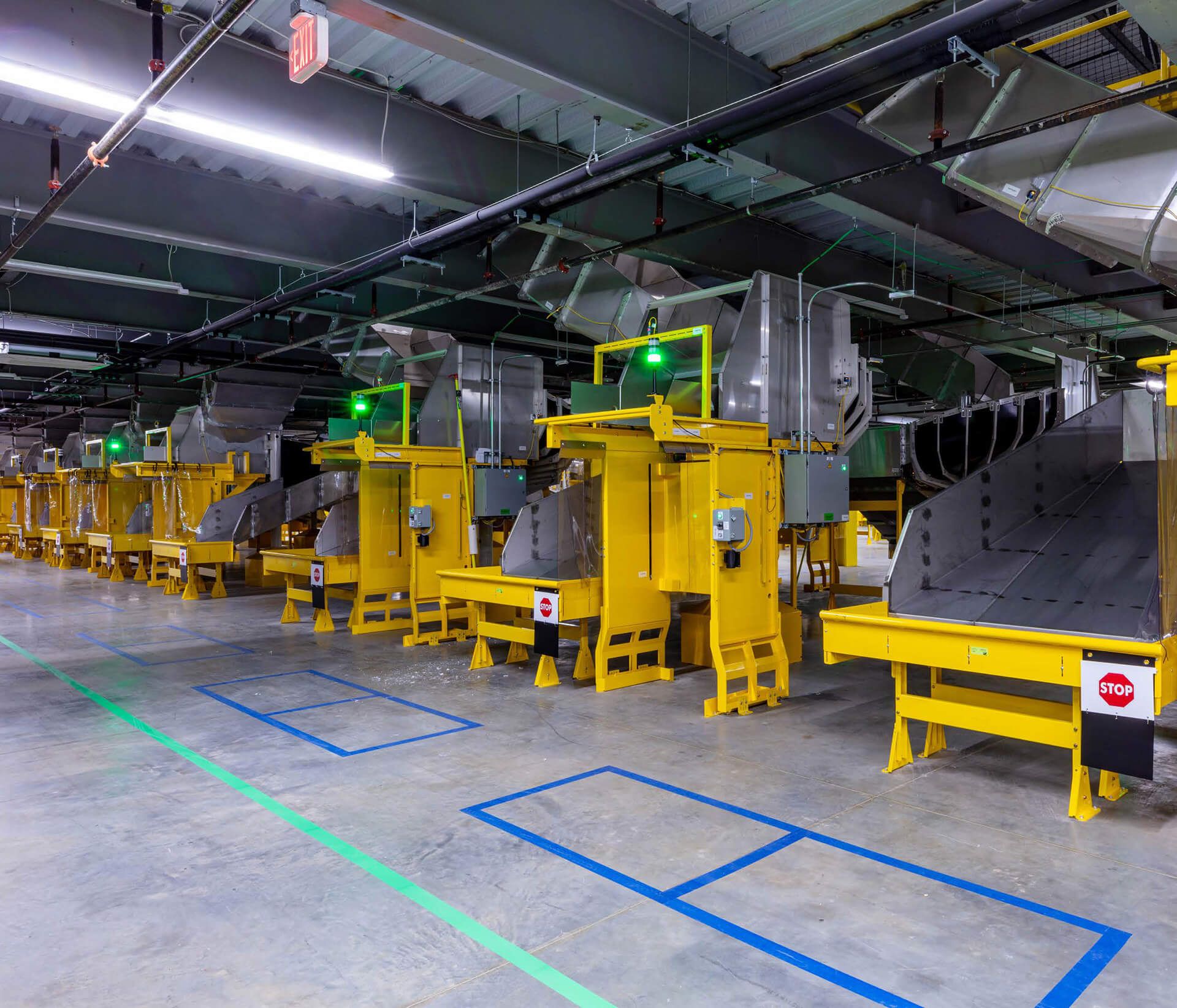
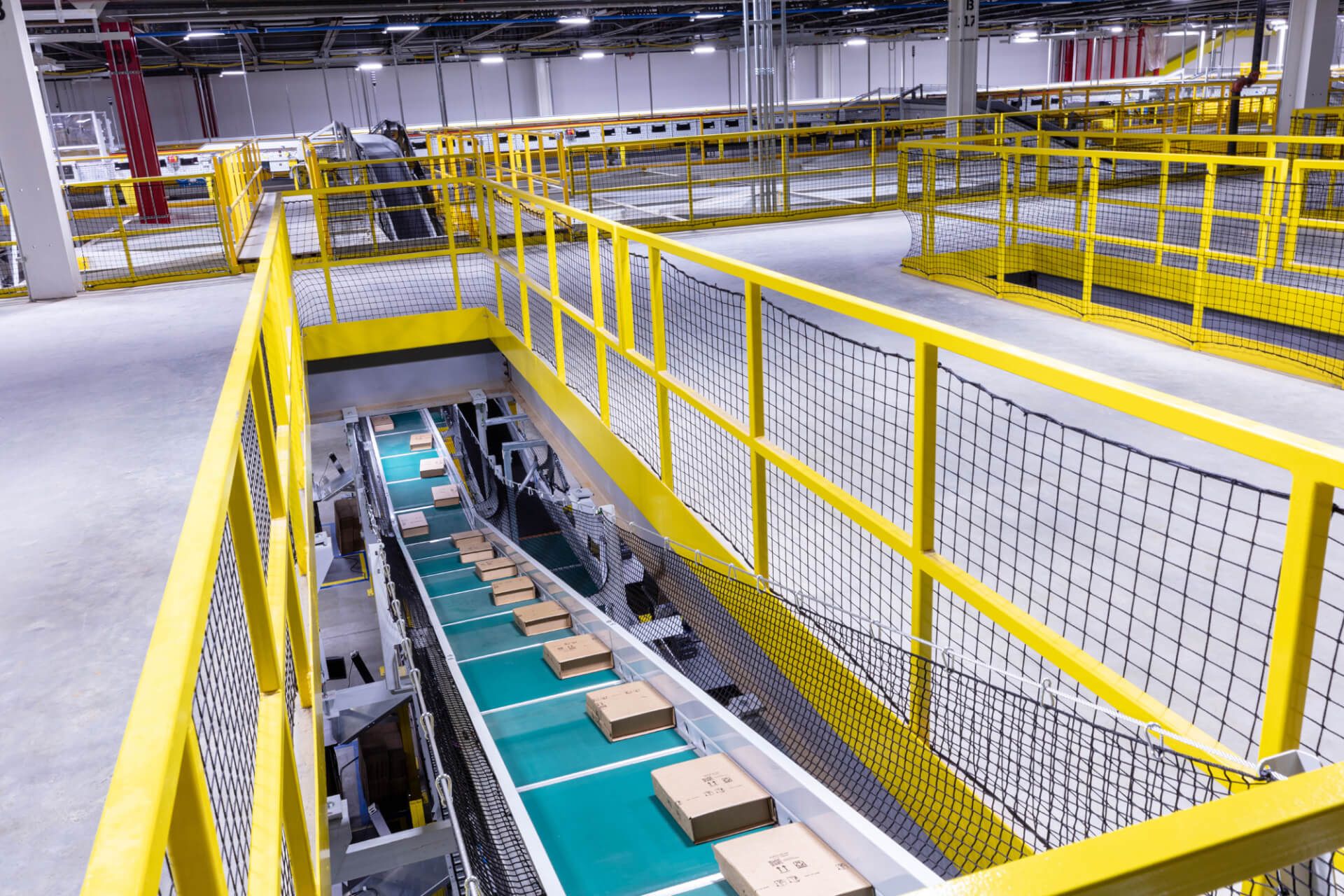
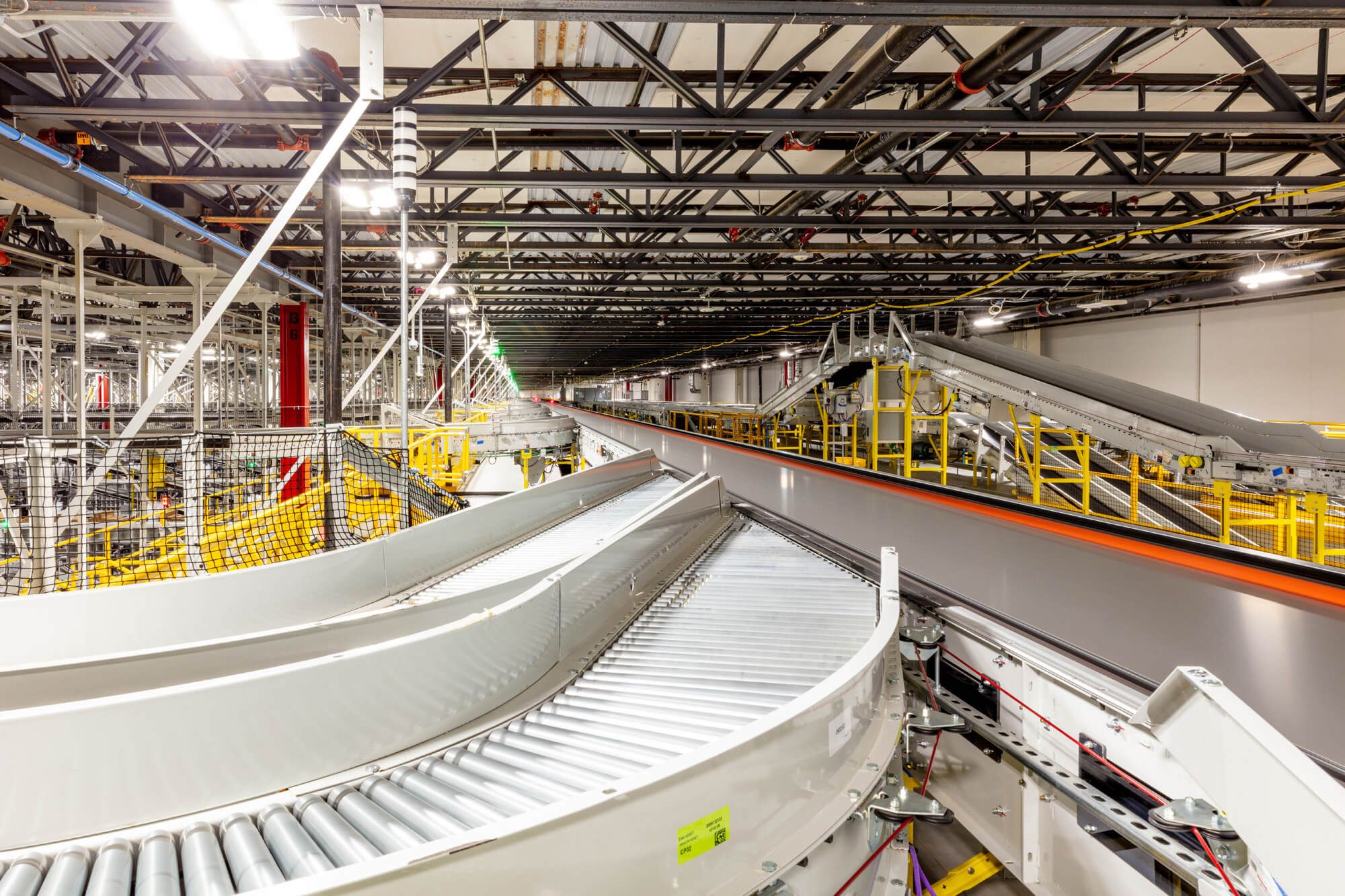
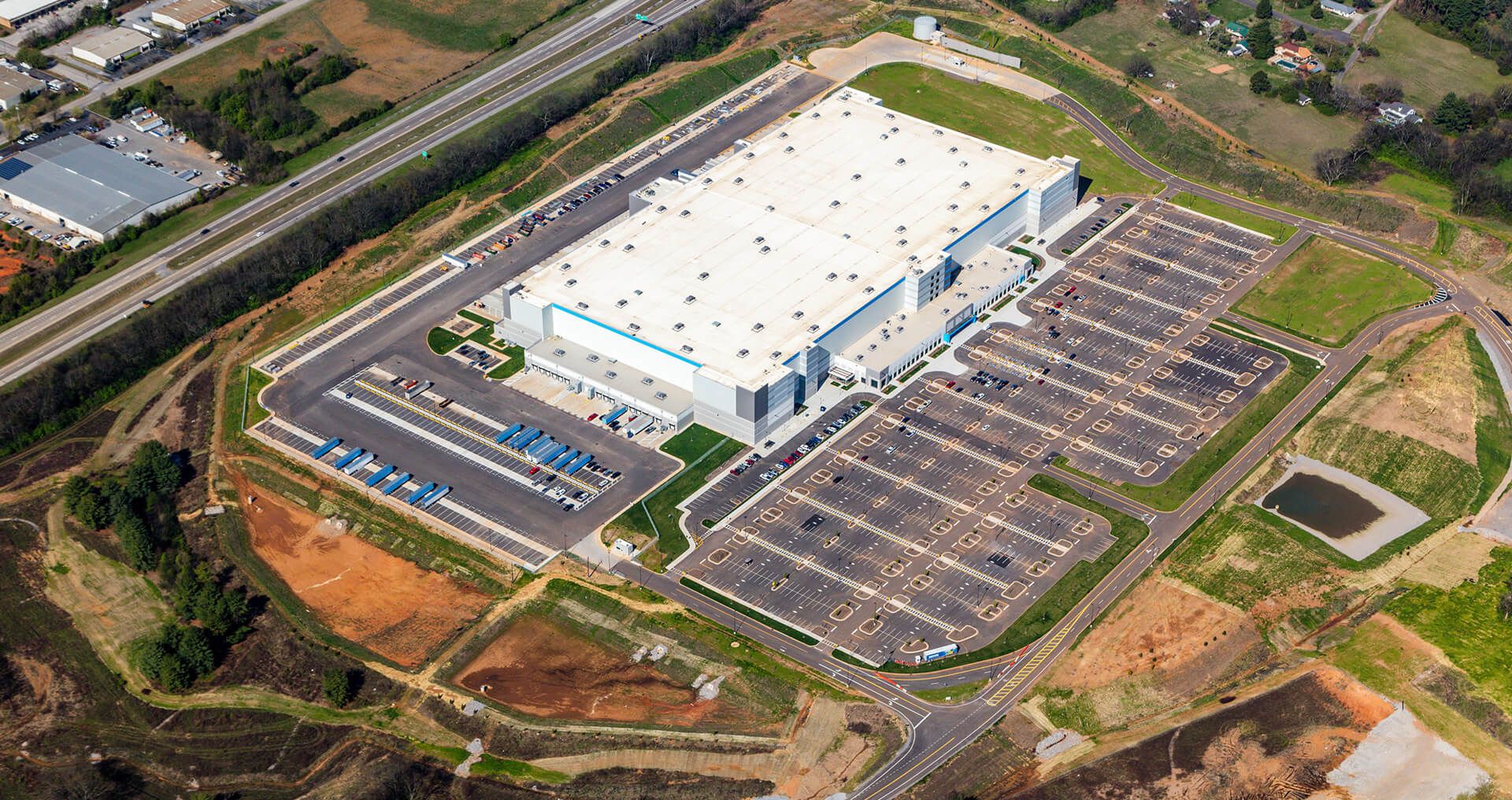
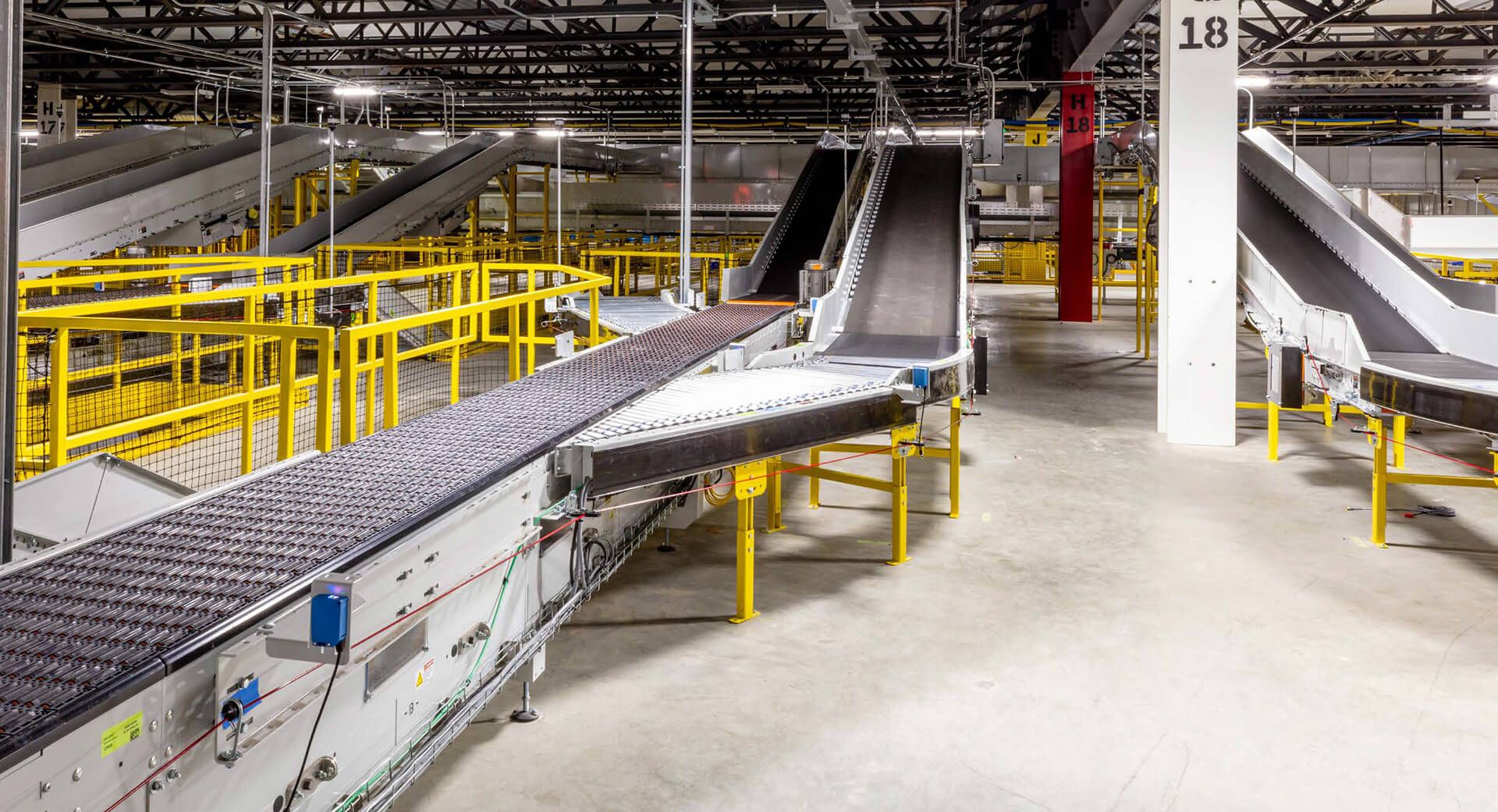
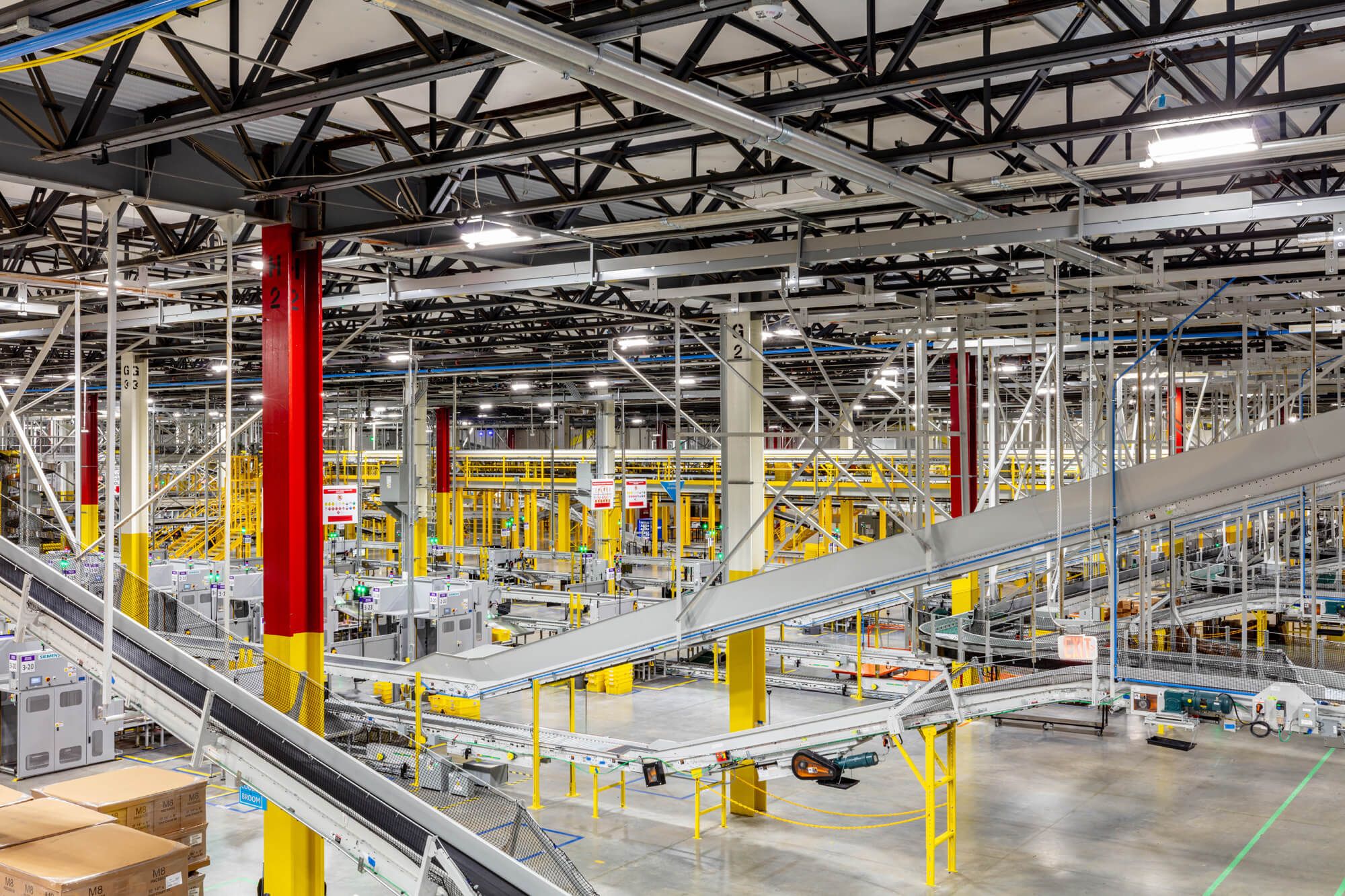
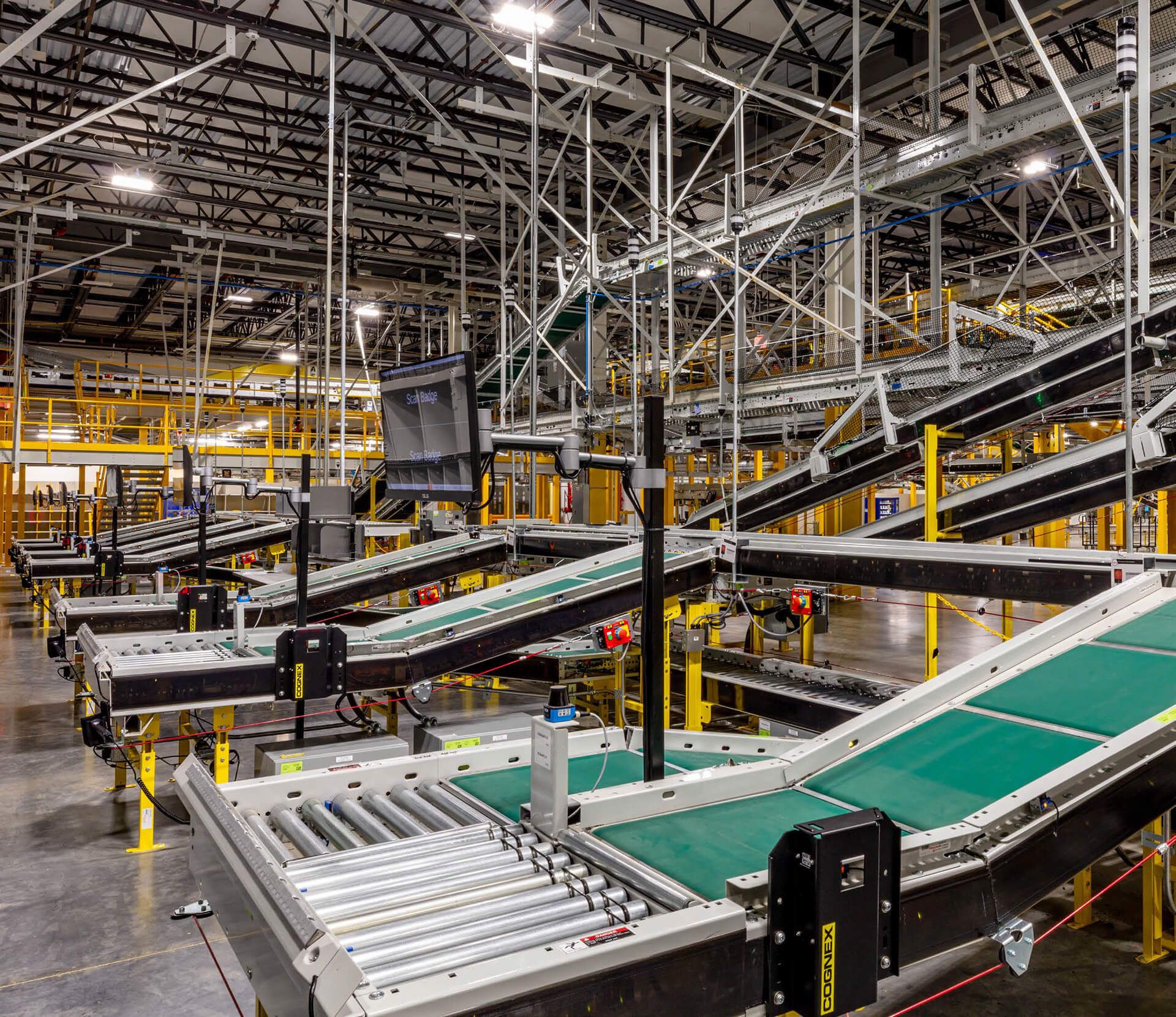
Delivering the Best Under Any Circumstances
Building During a Pandemic
We tracked the cost history, escalation, and lead times for critical materials that yielded an overall indication of future construction costs.
Based on our overall analysis, we initiated a strategic buy-out plan that awarded and locked in trade partner pricing as soon as it made sense for the project.
Working in teams is typically the best safety practice, and these measures ensured that workers could do so while socially distancing themselves.
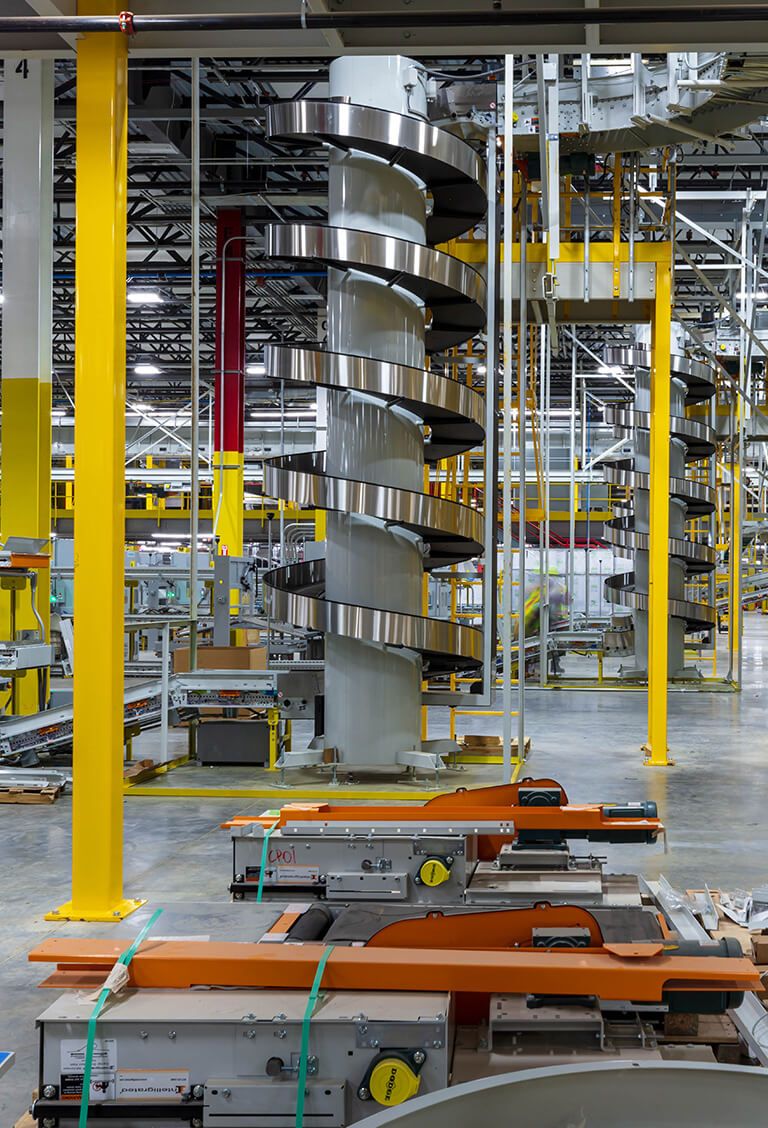
The Benefits of Experience
Since construction overlapped with a similar facility for this client, we created a tracking mechanism paired with weekly check-ins between the teams building the two facilities.
Creating collaboration among the teams ensured that efficiencies were maximized, lessons learned were incorporated, resources were streamlined, and the best cost and speed-to-market solutions were identified.
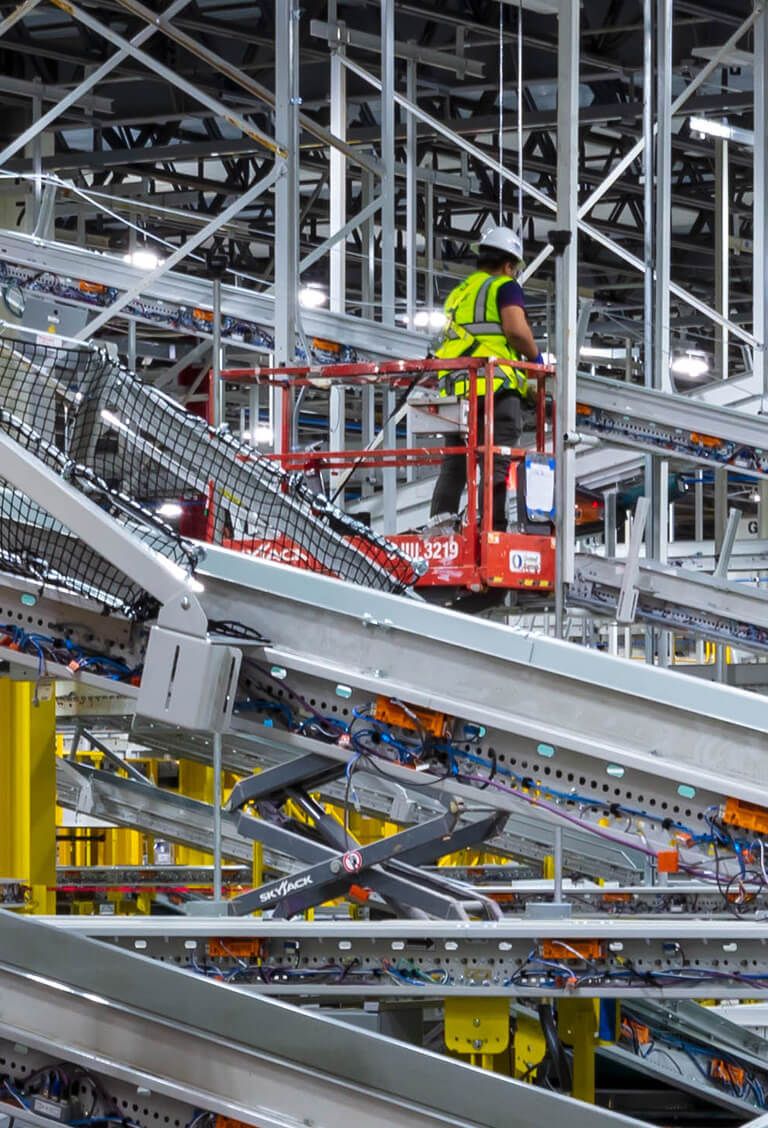
A Testament to Adaptability
Constructing during a pandemic while facing market and labor volatility presented a myriad of challenges. Combining in-house subject matter expertise, virtual design and construction (VDC) technologies, and Lean construction principles led to predictable progress, reduced costs, and an exceptional final result finished on schedule.
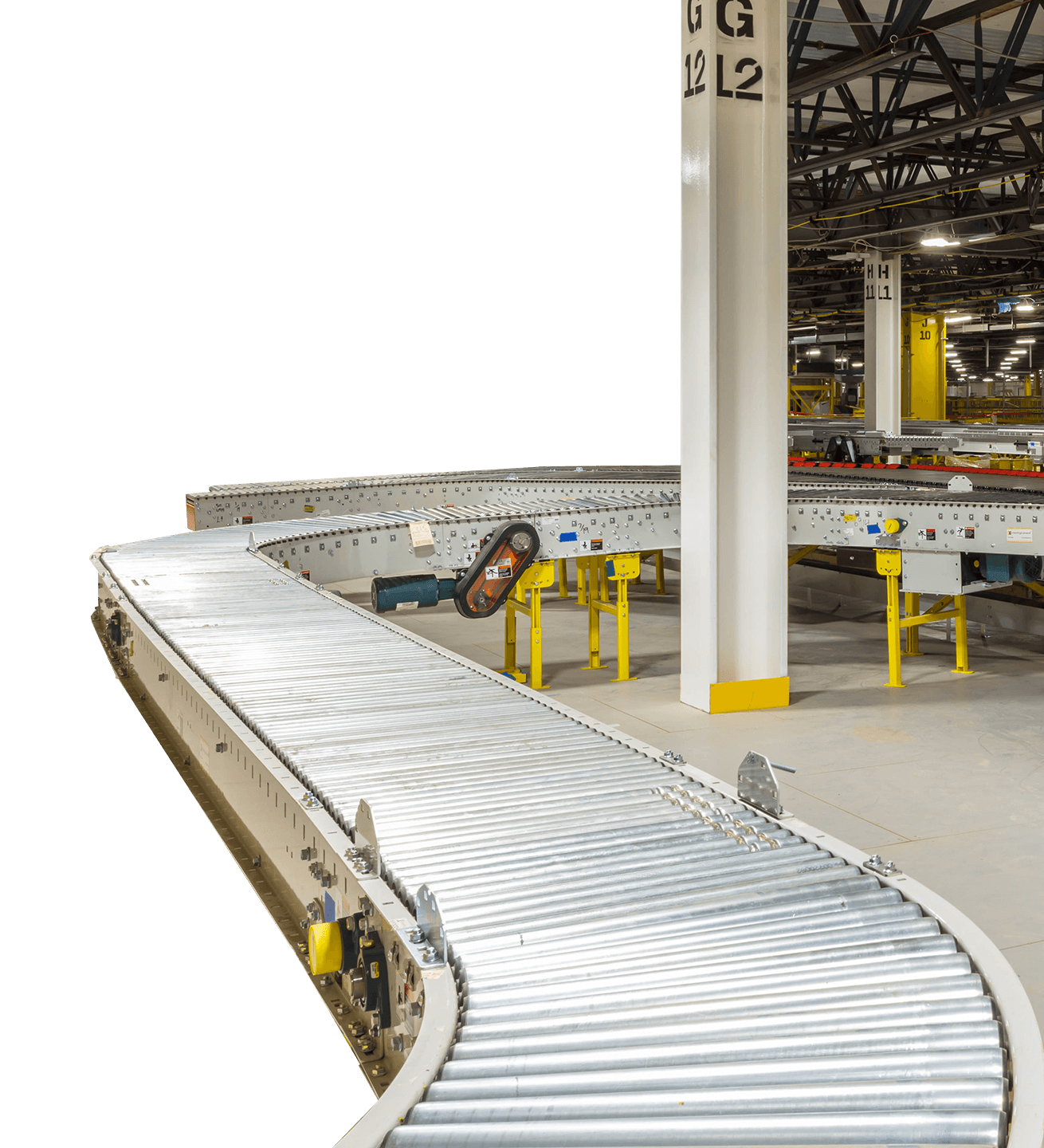
Project Overview
- Location
- Alcoa, Tennessee
- Size
- Confidential
- Industries
- Services
Highlights
- 1Nearly 30 miles of custom micropiles
- 2Virtual Design and Construction (VDC) resolved over 1,000 clashes during the preconstruction phase
- 3Leveraging existing client knowledge streamlined construction and resources
- 43.2 million cubic yards of concrete
- 519,000 tons of structural steel
- 69,000 tons of steel joist
Next Up
Hollywood Hard Rock
The ambitiously designed, guitar-shaped hotel is a symbol of the client and a triumph of modern building techniques.
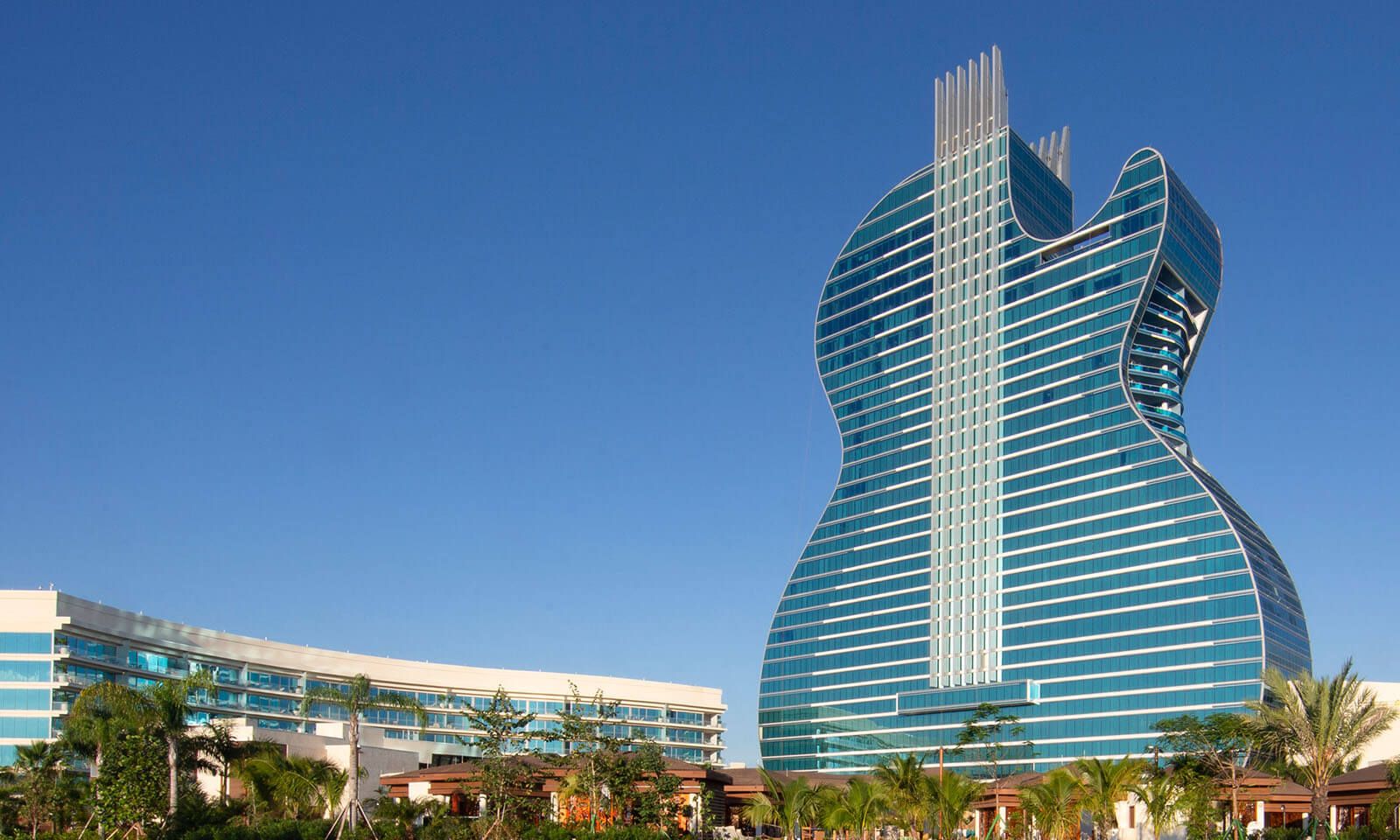